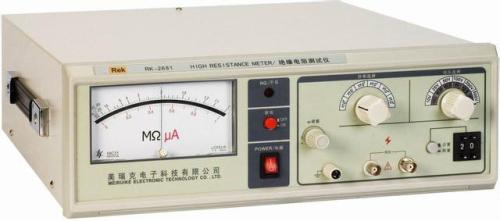
The position of micro-electromechanical (MEMS) technology in electronic products is increasingly important. Whether it is in the automotive, medical or military fields, such sophisticated components are needed. In the mass market such as information, communications and consumer electronics, You can see the rapid growth of MEMS applications.
MEMS is essentially a semiconductor technology that integrates micromechanical components (such as sensors, actuators, etc.) and electronic circuits on the same chip. The general chip only uses the electrical characteristics of the silicon semiconductor, while MEMS uses the electrical and mechanical characteristics of the chip.
Three-dimensional microelectromechanical systems (3D-MEMS), which process silicon into three-dimensional structures, packages and contacts are easy to install and assemble, and sensors made with this technology have excellent accuracy, minimal dimensions, and extremely low Power consumption. The sensor can be made from only a small piece of silicon and can measure three perpendicular accelerations. Examples include suitable mechanical damping for accelerometers and high-resolution altimeters that are subject to strong vibrations. The power consumption of such sensors is very low, which makes them have unparalleled advantages in battery-driven devices.
In a MEMS sensor chip, movement or tilt on three axes (X, Y, Z) causes a small displacement of the active silicon structure, causing a change in capacitance between the active and stationary components. The interface chip on the same package converts small capacitive changes into calibrated analog voltages that are proportional to motion. There are two typical analog sampling methods: electrostatic capacitance and piezoresistive. The former has advantages in terms of low power consumption and consumes less current.
The integration of MEMS and CMOS process technology has successfully driven the emergence of component products in consumer electronics applications. Semiconductor giants such as Intel, Samsung, TI, and TSMC are all optimistic about the development of CMOS MEMS, and have successively invested in the research and development of related technologies. While CMOS MEMS components can further reduce product development costs, 3D MEMS packaging technology plays a key role.
In addition to solving the technical bottleneck, 3D packaging technology can further integrate various components such as analog RF, digital Logic, Memory, Sensor, mixed signal, and MEMS under heterogeneous integration characteristics, and this integrated component can not only shorten the signal transmission Distance, reduced power consumption, can also significantly increase the speed of signal transmission. In addition, due to the 3D stacking method, the highest chip capacity can be achieved at a fixed unit volume in Form Factor.
With the rapid rise of MEMS technology in consumer electronics applications and the near-limits in semiconductor manufacturing, the integration of MEMS and CMOS processes through TSV technology has gradually attracted attention. Because 3D MEMS implied heterogenous integration features with multiple advantages such as low cost, small size, multi-function, and high-efficiency, it is expected to set off another wave of technological application revolution in the future and bring greater development to CMOS MEMS. Business.
Looking ahead to the development prospects of related products and technologies, the industry has begun to accelerate the layout of CMOS MEMS+3D MEMS Packaging solutions. The development of stacking Chips into 3D ICs in TSV mode is promising, and it is also expected to drive the rapid growth of 3D TSV Wafer shipments, differentiated by component categories. Currently, CIS (CMOS Image Sensor) uses TSV and IC 3D. The fastest, the second phase is expected to be played by memory (including Flash, SRAM, DRAM). 3D MEMS is expected to rise in 2011 and stabilize toward commercialization in the next three years. Most of the MEMS products are produced on an 8-inch wafer of 150mm to 200mm. It is expected that the MEMS products will gradually be transferred to a 300-mm 12-inch plant in the next six years in order to make optimal use of capacity.
Iron Battery,Nife Batteries Australia,Nife Battery 600Ah For Asutralia,Ni-Fe Battery 450~600Ah
Henan Xintaihang Power Source Co.,Ltd , https://www.taihangbattery.com