Volkswagen announced the recall of an electric golf car (e-Golf) sold in the United States some time ago because its battery management system may use internal current surges as current critical conditions, causing the vehicle's electric motor to suddenly turn off. First let's take a look at the battery structure of Volkswagen.
This article refers to the address: http://
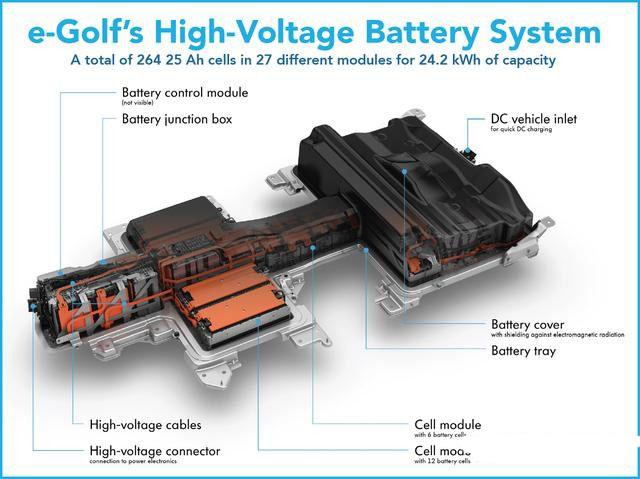
The high probability here is that the battery management system detects a high current pulse and then protects it. The level of this fault defines a high price.
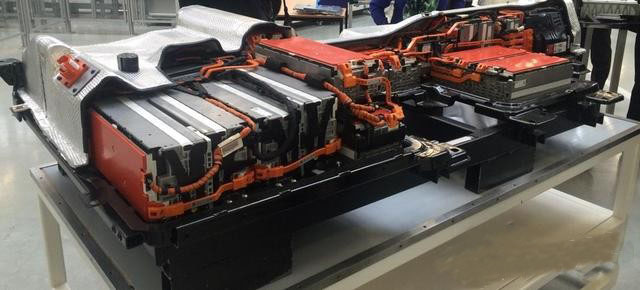
When we consider this matter, we can take a look at the structure of the German system. In fact, it belongs to the battery management system to a relatively high level (BMS main module ASIL C).
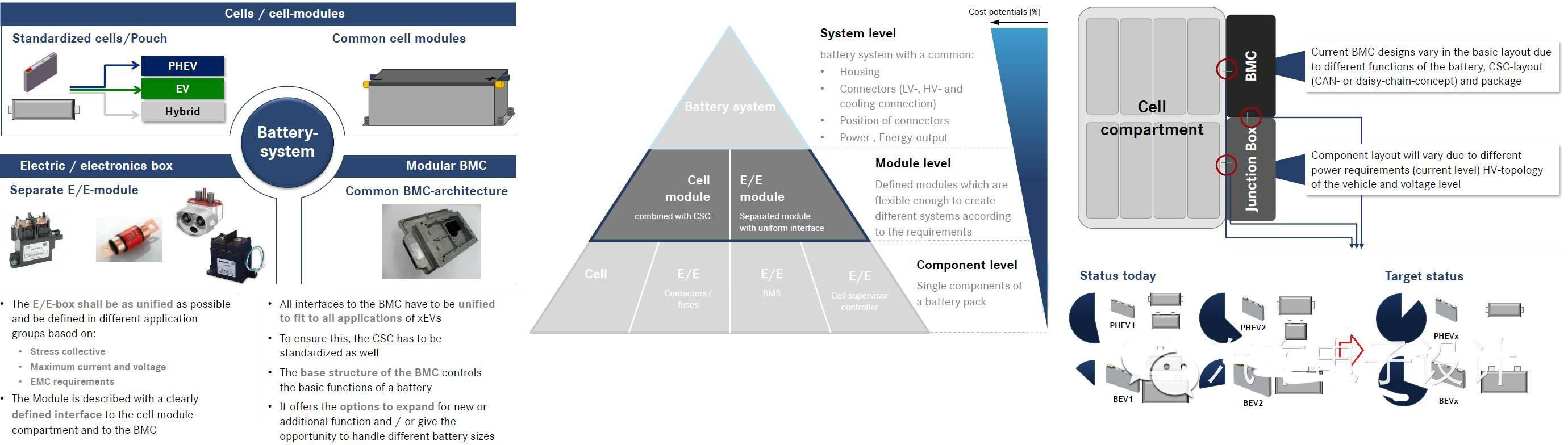
I think that many algorithms of BMS can be directly placed in the VCU. We do the following analysis:
a) Measurement function:
1) Basic information measurement: battery voltage, current signal monitoring, battery pack temperature detection The battery management system has the most basic function is to measure the battery cell voltage, current and temperature, which is the top calculation and control logic of all battery management systems. basis.
2) Insulation resistance detection: Insulation testing of the entire battery system and high voltage system is required in the battery management system.
3) High-voltage interlock detection (HVIL): used to confirm the integrity of the entire high-voltage system, when the high-voltage system loop integrity is damaged, start safety measures.
b) Estimation function
1) SOC and SOH estimation: the core is also the hardest part
2) Equilibrium: When the SOC × capacity between the cells is unbalanced, the adjustment is performed by the equalization circuit.
3) Battery power limitation: The battery has a certain limit on the input and output power at different SOC & temperature.
c) Other functions
1) Relay control: including main +, main -, charging relay +, charging relay -, pre-charge relay
2) Thermal control
3) Communication function:
4) Fault diagnosis and alarm
5) Fault tolerant operation
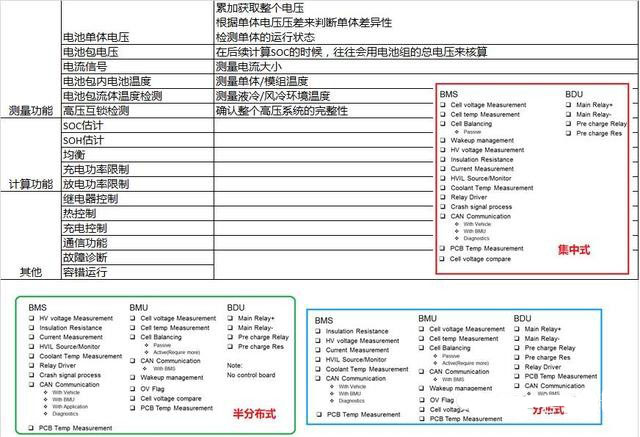
For detailed, you can see the following picture:

Proportion of software for a complete BMS
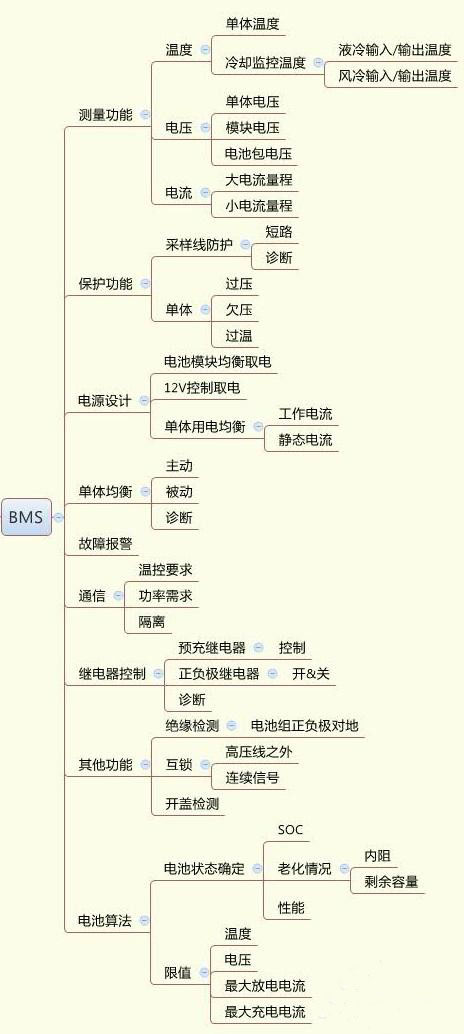
I personally feel that the future direction of development is:
1) Reserved function
a, monomer related functions (voltage, current and temperature measurement & protection)
b, balanced execution circuit
c, communication
d, minimum diagnosis and minimum record
2) Transfer function
a, SOx algorithm and power limitation
b, high pressure measurement
c, relay control and diagnosis
d, thermal management control
The main reason here is that, in fact, if BMS does SOC and SOH, it has higher requirements for the computing power of BMS. BMS needs to consider the safety of the whole vehicle. In fact, all the estimates are still placed at the VCU level for troubleshooting. . The question is coming, why don't we deal directly with the VCU?
Comparison
a, VCU can be obtained from the entire bus network, the voltage at each point (inverter, power distribution box, battery pack)
b, VCU can obtain the main battery pack current and inverter current, if the former fails, try to turn off HVAC to infer the whole current
c, the VCU lacks the problem in the battery pack, but can be estimated based on the temperature of multiple points.
d, VCU itself is a very high-level component
The benefits of this are:
a, the function inside BMS can be done very simple
b, BMS can be completely modularized in different places
c, BMS will completely reduce the level of the manufacturer, can be corrected in the VCU to achieve multi-vendor switching
d, BMS and modules can also be separated
e. In theory, such cost and IP are better.
f, such car companies are fully responsible for battery life and warranty, need more monomer and module data
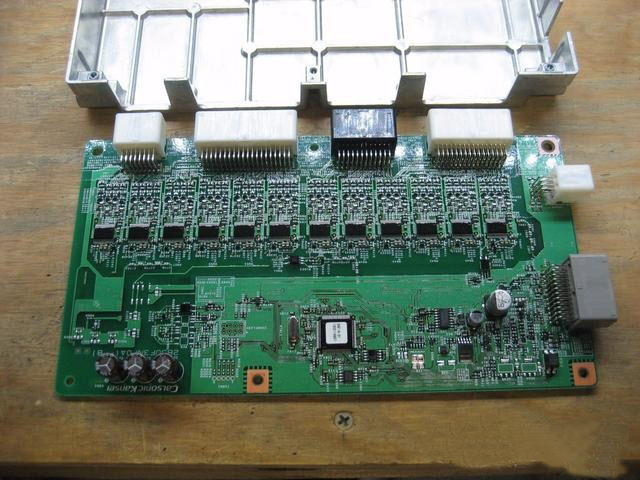
As shown in the following table:
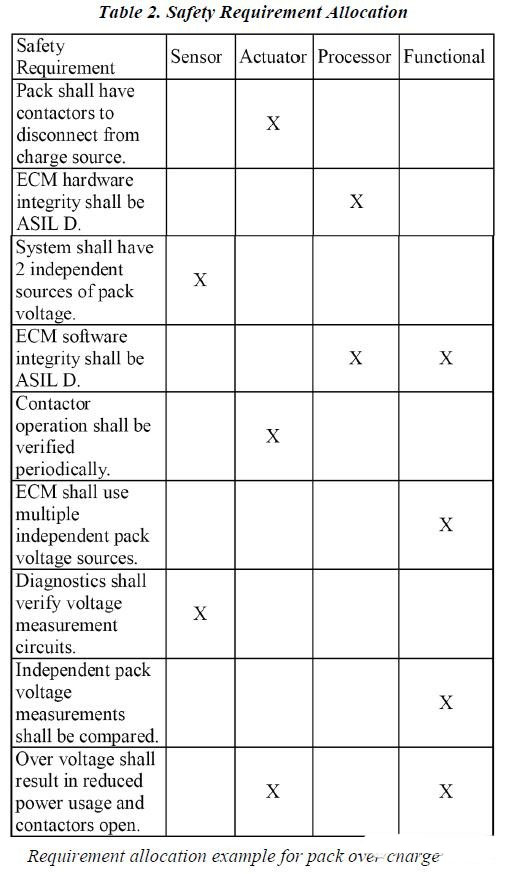
summary:
1) I believe that the future will become very simple. So many companies in BMS are completely abnormal. The car companies will eventually master the actual situation of the battery and analyze the later data and the previous test data. This cycle is not available in the battery factory.
2) In theory, this kind of brush writing does not involve the battery manufacturer, and the response speed is also faster.
Screw Terminal Connector,Pcb Screw Terminal,Screw Terminal Block Connector,Screw Type Terminal Blocks
Cixi Xinke Electronic Technology Co., Ltd. , https://www.cxxinke.com